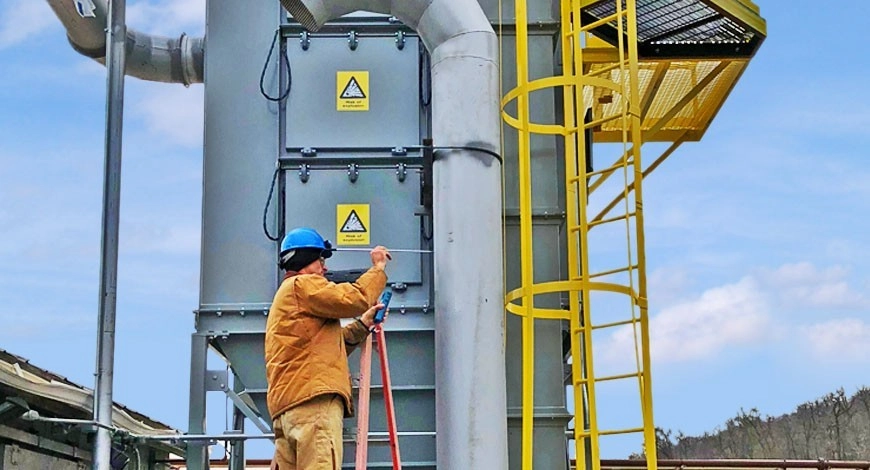
Dust Collectors: Focus on Preventive Maintenance
When purchasing the latest dust collector, many companies make a fatal mistake: they skimp on maintenance, either due to a lack of information, or sometimes out of negligence. Companies may think they’re saving a few bucks, but in reality, they’re heading down a costly—and dangerous—road. Oh, the horror stories our experts could tell! Let’s explore the various issues that can arise in an improperly maintained dust collector.
Moisture In The System
The dust collector’s Enemy No. 1, moisture can wreak havoc if the recommended preventive methods are not applied.
In The Cleaning System
Companies purchasing a dust collector sometimes think it’s not necessary to install a desiccant air dryer, for example. Although the standards don’t require this component, it plays a key role in damage prevention.
Placed between the compressor and the air tank, a desiccant dryer removes excess moisture from the ambient air. When running a cleaning cycle without an air dryer, the high velocity of compressed air causes a drop in temperature, and any moisture in the air immediately condenses.
Translation: what’s passing through the filters is no longer air, but water! Certain dust particles will then build up on the filters, acting like a glue that the cleaning system cannot dislodge, and eventually clogging the filters prematurely.
At The Dirty-Air Inlet
Air naturally has a certain moisture content that is often higher inside a plant, especially when rotary dryers or ovens are part of the production chain. In its gaseous state, this moisture is manageable inside the dust collector, as long as the temperature does not fall below the dew point. However, if that happens, the moisture in the warmer air will condense onto the colder interior metal walls, eventually causing rust to form and shortening the life of the dust collector.
One solution to this problem is to thermally insulate the dust collector. This way, the temperature can be kept high enough to prevent condensation. Depending on the source of the problem, an electric coil that heats the dust collector walls can also be added.
If the problem was not detected at the time of the dust collector’s design or installation, or if conditions have since changed, regular preventive maintenance can give specialists a chance to recognize the warning signs and offer a tailored solution.
Air Tank Pressure
Filtration media can also be damaged by excessive air flow. As a general rule, air pressure in the tank should be between 550 kPa and 700 kPa. This air tank is used to clean filtration media to prevent dust build-up. You may therefore think that increasing the air pressure will clean the filters better and make them last longer. But it’s exactly the opposite!
Too much air pressure can dislodge the dust cake that protects the system. Without this dust cake, filtration media are more vulnerable and break down more quickly. Excess pressure can also damage filter fibers, creating dust leaks that contaminate the clean airflow exiting the dust collector. This is especially problematic when the air is being recirculated within the facility.
Excess compressed-air pressure can also rupture diaphragm valves. Made of flexible material, these valves can crack, causing an air leak. Insufficient air supply to the blow pipe also reduces the cleaning efficacy of the rows of filters.
In turn, the restricted airflow across improperly cleaned filters increases the differential pressure, affecting the dust collector’s overall performance. Over the long term, if damaged diaphragms are not replaced, the rows of filters could become prematurely clogged and have to be replaced.
If there is an air leak or increased pressure in the tank, the compressor has to work harder to compensate, the fan motor runs more, and the system consumes more energy.
Excessive Fan Vibration
Torn filters can lead to unforeseen expenses, but it’s when the domino effect reaches all the way to the fan that the damage becomes serious – and costly. A dust leak draws particles through to the fan blades. If the particles are hydrophilic and there is moisture in the airflow – as is often the case – the dust may stick to the blades1, creating an abnormal vibration. (Imagine the banging of a washer drum with unevenly distributed clothes inside). Over the long term, this vibration damages the entire fan, starting with the blades scraping against the inside walls2. If the problem isn’t fixed, the shaft3 and ball bearings are next to go. As you can see, these very costly repairs can easily be avoided with routine inspections or the installation of a broken bag detector.
On the other hand, this scenario can easily turn to disaster if the fan in question is not to the AMCA Standard for Type C construction. This standard requires aluminum disks to be installed between the fan blades and the inner wall to prevent sparking when the blades scrape the inner wall. Add combustible dust particles to this mix and you have all the conditions necessary for an explosion.
Debris
Another situation occurring more often than you might think is the build-up of debris in the dust collector. Screws, bolts and drill bits can accidentally be sucked in. Some people even treat the dust collector like a garbage bin. (Our specialists have even found 2x4s thrown in!) Whether it gets there accidentally or intentionally, debris in the dust collector can have disastrous consequences. Metal parts can pierce the bags and filters or create sparks if they scrape against the steel walls. Larger debris blocks the blow back dampers, which prevent flames from shooting back into the plant in the event of an explosion.
If the debris travels farther down the system, it can end up in the hopper’s rotary air lock and block or damage it. If this happens, the space separating the air between the hopper and the barrel is no longer sealed. Imagine a bolt being propelled into the ductwork at high speed, causing sparks and, in turn, creating an explosion. The inside of the dust collector will catch fire, and a chain reaction will follow. The dust built up in the barrel will fuel the fire, increasing the scale of the disaster because, with a damaged rotary air lock, neither section is airtight anymore. Even with no debris, the air lock’s integrity can be compromised by normal wear of the rubber extensions on the blades.
Dust Build-Up
Every day, your dust collector discharges a certain volume of dust into the barrels (or other receptacle). After some time, these barrels obviously need to be emptied, otherwise the dust could back up into the hopper, block the rotary air lock and even clog the filters. Besides affecting the system’s performance, this build-up poses serious risks of contamination or explosion, depending on the type of dust particles. Despite its best efforts, your team could be misled by a sensor that is defective or unable to measure fine particulate matter. Your daily maintenance routine should therefore include checking this sensor to confirm that it is detecting the actual volume.
Fortunately, all of these types of deterioration can be resolved if a technician catches them in time. Most of them are detectable through certain warning signs that an experienced eye can recognize. Extend the life of your dust collector by calling our preventive maintenance specialists.