Pharmaceutical
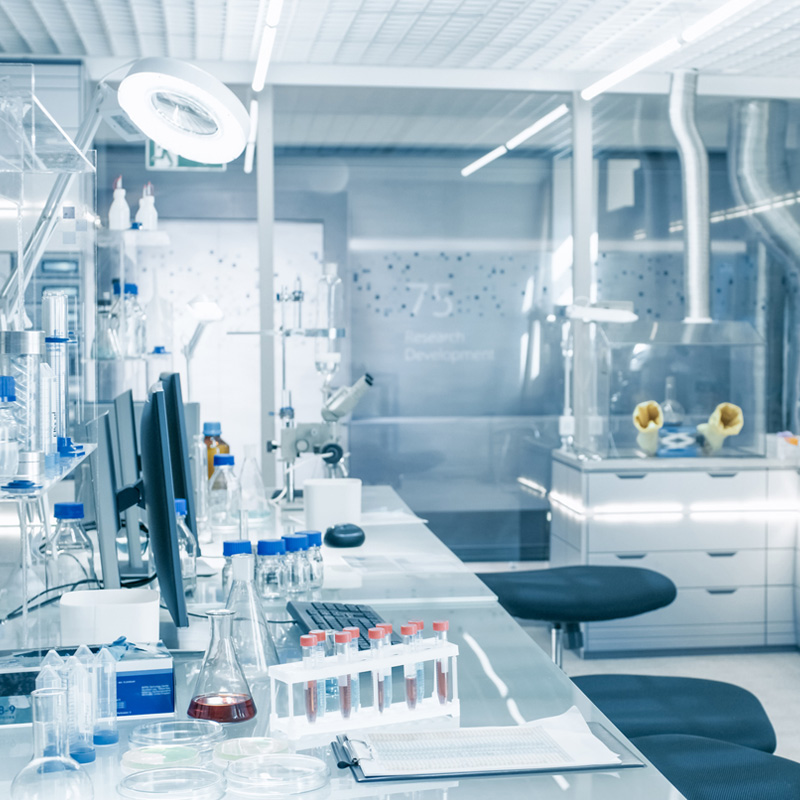
The Pharmaceutical Industry and Its Contaminants: What Do You Need To Know?
When pharmaceutical products are manufactured, powders and pigments are gently handled on a daily basis. You must factor in many parameters when developing and designing your dust collection and ventilation systems. Consider these factors:
- Do you have adequate control over your internal environment, particularly in the cleanrooms? Temperature, moisture and pressure are aspects to be monitored, as are the airflow characteristics.
- Your processes generate multiple types of particles that can create potentially harmful and explosive chemical mixtures; are you equipped to control the spread of them and reduce the risk of deflagration?
- Do your capture measures effectively prevent the proliferation of airborne micro-organisms or bioaerosols?
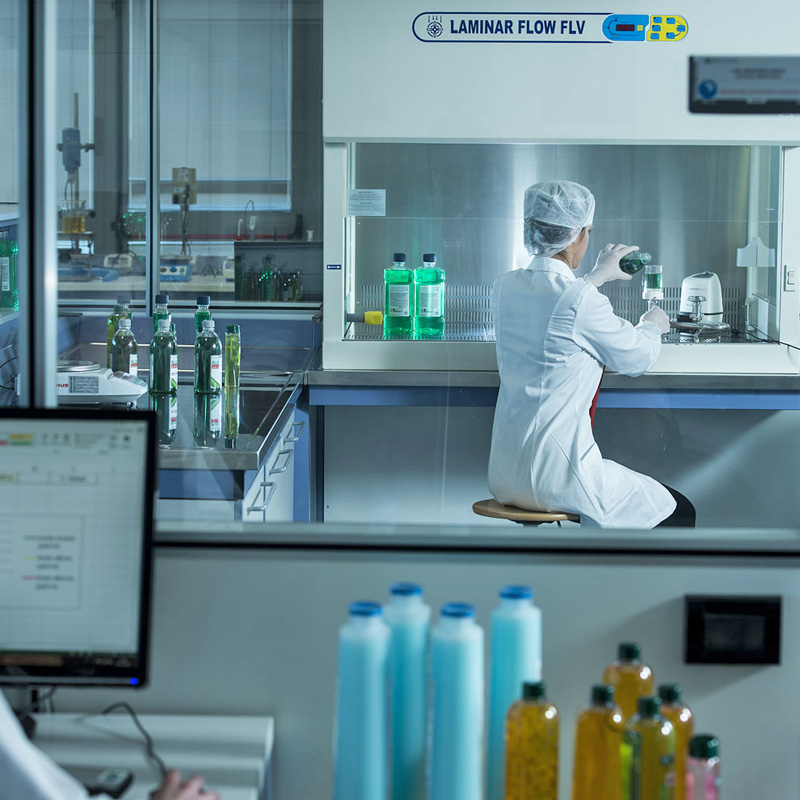
Are you aware of the risks associated with your processes?
You know as well as we do that your industry has its share of constraints. When you manufacture medications or other pharmaceutical products, you must deal with risks associated with particle, dust and bioaerosol emissions, while reducing cross-contamination. For example, contact between certain contaminants could cause a chemical reaction that triggers a fire or explosion. In addition to your processes, your facility’s air handling is important — from laboratories to storage — in order to prevent the products from breaking down.
The retention capacity of the filters in your dust collector is also an important aspect of your system’s performance. Another aspect is maintenance. Depending on the model, you will need to reduce human contact with the contaminated filter medium when replacing its filters or emptying the hopper under the dust collector. An additional challenge: preventing the particle-laden air from escaping during that maintenance. Among the various ways of protecting the workers’ breathing zone, replacing the filters with a "Bag-In/Bag-Out" solution can reduce this risk.
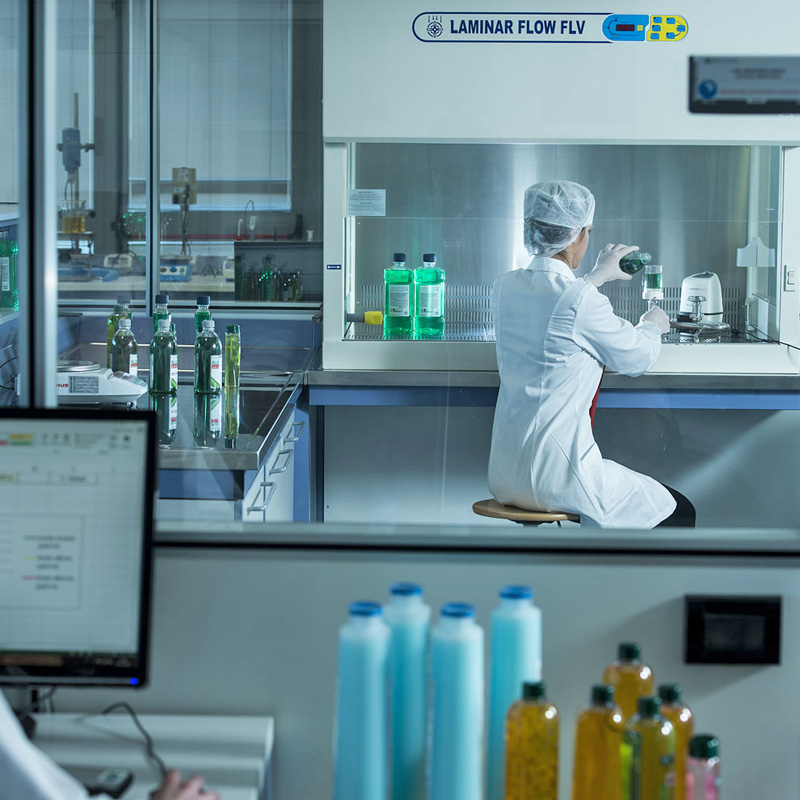
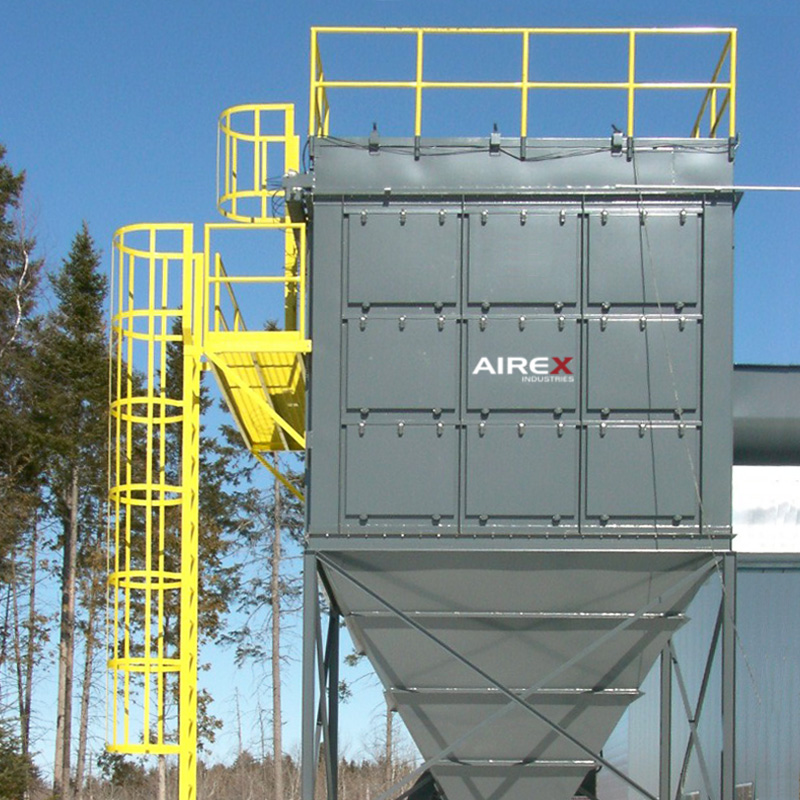
How can you reduce the risks of fire and explosion?
In the pharmaceutical industry, some of the substances involved are extremely combustible, such as organic particles. Our experts can suggest effective dust collection and prevention solutions for you that meet the standards in effect. You will be able to reduce the risks of fire and explosion in your laboratories and when handling chemicals (in keeping with the NFPA 45).
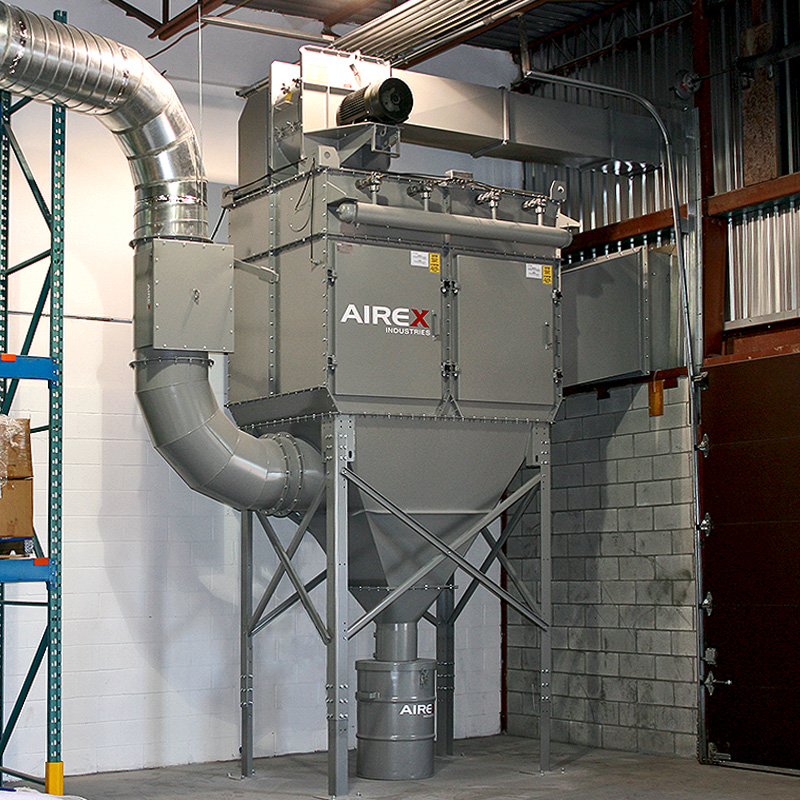
What Is The Best Dust Collector For The Pharmaceutical Industry?
Every player in your industry has unique issues, which is why we can’t recommend a one-size-fits-all solution! In the presence of fine dusts, micro-organisms or bioaerosols, HEPA – ULPA is a good option. Did you know that a ULPA filter, which is found in the air shower, filters out 99.99% of the micro-droplets of microbes? With encapsulators, it is also possible to capture the particles at the source, without absorbing the product introduced into the capsules, in particular by creating a negative-pressure environment.
We believe that the best dust collector is the one that perfectly meets your needs. The system must also enable you to save you money. Our experts can suggest some sustainable options for you that are well thought out to minimize production shutdowns, repairs and obviously energy consumption. Here is a quick look at what we can offer you:
- Innovative solutions with an excellent service life, such as our ambient temperature control system for laboratories and storage areas.
- Equipment approved by the NFPA standards for preventing incidents.
- A team consisting of engineers and specialists is available to you for breakdowns and preventive maintenance.
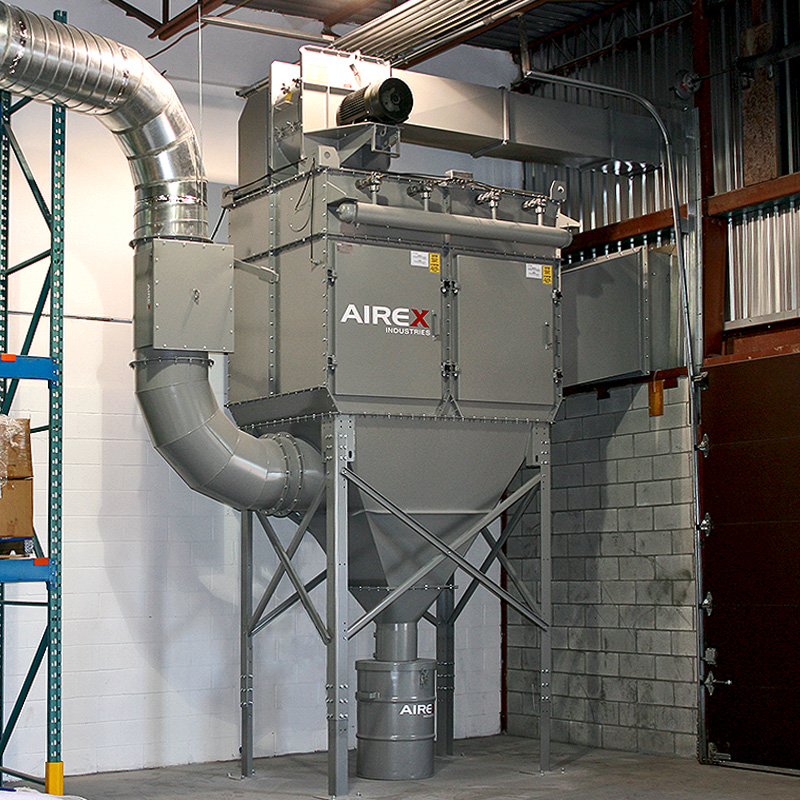